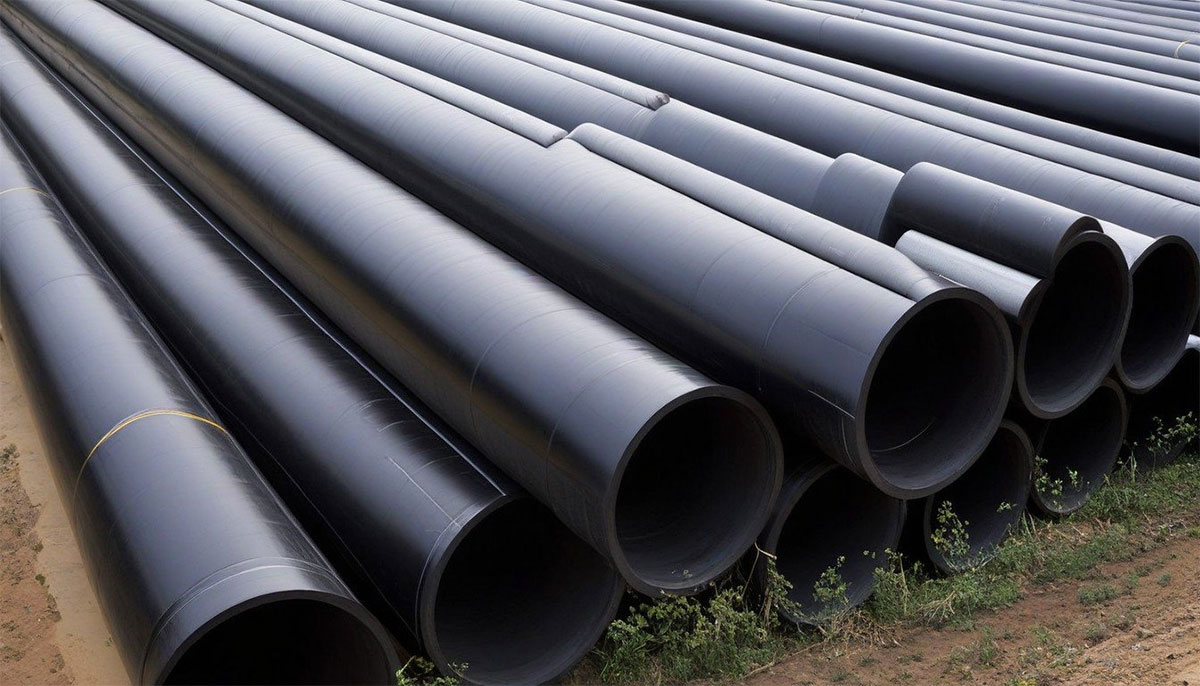
Getting to know the testing methods of polyethylene pipes
Polyethylene pipes are used as one of the most important elements in fluid transmission systems in industry and irrigation, water supply, gas and oil systems. But how can we make sure that these pipes have the necessary quality and use them in the best way?
Polyethylene pipe tests play a very important role in ensuring the safety and optimal performance of these pipes. Conducting these tests during the production and use of polyethylene pipes assures consumers that they have a quality and standard product. For this reason, it is essential to know how to perform these tests and their importance for every person who uses these pipes.
Finally, raising public awareness about polyethylene pipe standards and tests is an important starting point to make better decisions in choosing and using these important products.
types of testing polyethylene pipes
In general, based on the requirements of the national standard of Iran under the number INSO 14427, the mandatory criteria are according to the table below, we will explain them further in the following
row | Required Criteria | Compliant test method | limit | |
1 | Appearance condition (visual inspection)
| 14427-2 paragraph 5-1 | – | |
2 | Markup | 14427-2 paragraph 11-2 | 1.5 meters | |
3 | Qatar | Mean outer diameter | 14427-2 Table 1 | According to the standard table |
Maximum double width | 14427-2 Table 1 | According to the standard table | ||
4 | Thickness | Minimum thickness | a14427-2 Table 2 | According to the standard table |
max thickness | a14427-2 Table 2 | According to the standard table | ||
percent thickness changes (tolerance) | 14427-2 | According to the standard table | ||
5 | Density | Density of raw material | National 7090-1 (test method) and table one of standard 1-14427 | greater than or equal to gr/cm30.941 |
tube density | National 7090-1 | greater than or equal to gr/cm30.941 | ||
6 | MFR | MFR material | National 1-6980 and contract provisions (test method) and table one of standard 14427-1 | 0.7 ≥ ≥ 0.15 |
MFR pipe | National 6980 and contract provisions (test method) and table one of standard 1-14427 | 0.7 ≥ ≥ 0.15 | ||
Deviation of MFR value of tube with raw materials (%) | 14427-2 Table 5 Permissible limit: 20% nominal deviation | ±%20 | ||
7 | Soot amount | ISO6964 | 5-2.2% by weight | |
8 | Soot scattering | degrees | ISO18553 National Standard 20059 | B or A1 A2 A3 |
Soot dispersion rate | ISO18553 National Standard 20059 | rate less than or equal to 3 | ||
9 | Hydrostatic consolidation | 1-12181, 2-12181, the national standard must comply with table 3 of the national standard 14427-2 | 20 degrees 100 hours 80 degrees 165 hours | |
10 | longitudinal return | ISO9505 | Less than or equal to 3%, the initial appearance of the pipe should be maintained | |
11 | Thermal stability (OIT oxidation induction time) | INSO-7186-6 | Greater than or equal to 20 minutes | |
12 | Strength test | ISO6259 INSO-17140-1, 3 | Greater than or equal to 350% | |
13 | Other parameters and tests | According to the standard included in the documentation |
Melt flow index
melt flow index test (MFI, MFR or MIR) shows one of the rheological factors of polymers
set. This index is expressed in grams in ten minutes from a standard thread under a standard load (usually five kilograms) and at a standard temperature (190 degrees Celsius for polyethylene).
A high melt flow index indicates low molecular weight of the polymer material and low viscosity, while a low melt flow index indicates the presence of a viscous polymer.
For example, for heavy polyethylene in the pipe and fittings industry, the numerical value of the melt flow index for PE100 grade is around 0.2g/10min at a temperature of 190 degrees Celsius and a weight of five kilograms. And for PE80 grade, it is usually around 0.4g/10min with the same temperature and load. For light polyethylene or irrigation pipes, this amount is about 0.3g/10min with the same temperature, but the weight is 2.160 kg. Therefore, its results can be mentioned as a suitable test and reference for distinguishing and comparing polyethylenes from each other.
Polymer material in the extruder is affected by shear forces and melts. Therefore, the value of the melt flow index will always be different from the ratio of the declared value of the melt flow index in the analysis sheet, which is performed by the melt flow index tester and only by applying vertical and pressing forces and without the presence of shear forces, and this amount of difference for pipes Polyethylene is 20% for water supply and 10% for gas supply.
If the difference is more than these, the product often suffers regional burns, as a result of which the quality characteristics of the final pipe are greatly reduced.
The national standard for this test for polyethylene pipes is INSO 6980-1.
Tension test
Nowadays, most polymer materials have found many uses due to their desirable physical and mechanical properties. Therefore, to use these materials, we require basic knowledge of their mechanical behavior. One of the tests used to identify the mechanical behavior of polymers is the cold tensile test (without applying heat) in a device with the same name. In this test, a dumbbell-shaped sample is prepared from a polymer sample with standard dimensions by a milling machine or cutter press. This sample is placed between two clamps of the machine and is stretched at a constant speed (from 10mm/min to 100mm/min). Meanwhile, a stress and strain diagram is obtained by the device software.
Samples made from brittle materials such as metals break suddenly due to stretching at a certain stress value. While for soft and malleable polymer materials such as polyethylene, when the stress increases, the sample undergoes yielding and begins to strain or increase the percentage of length. The area where we see the yield stress is the so-called neck. As the polymer is stretched, this area changes and becomes thinner.
As the deformation continues, the neck region becomes longer and continues until the stress reaches its ultimate tensile strength and the specimen ruptures.
The minimum percentage of elongation or strain for polyethylene pipes for water supply purposes is at least 350%, while for gas supply purposes, this number must be greater than 450%.
The national standard for this test for polyethylene pipes is INSO 17140-1,3.
Soot percentage test
One of the best alternatives to steel and concrete pipes intended for the transportation of water and natural gas is the polyethylene pipe, which, due to its excellent versatility, Its chemical resistance and strength.
But it should be kept in mind that studies have shown that long-term exposure of polyethylene pipes and fittings to ultraviolet radiation can affect its mechanical properties (change in polymer structure and creating cracks in polyethylene structures) will have a negative effect. Tests show that these tubes undergo a specific type of failure called slow crack growth (SCG) that occurs at low stress levels (below yield stress) and near room temperature. The mechanism of this failure includes the formation of cracks, their growth and the final propagation of the crack.
And this is a problem point for these polyethylene pipes that must be solved. The most widely used method of UV protection is the production of black polyethylene compounds with the addition of 2 to 2.5% uniformly dispersed carbon black, which significantly increases UV resistance indefinitely.
Adding carbon black is done in petrochemicals and before the granulation operation, or during pipe production by adding black masterbatch (ethylene bridge carrying 40% carbon black) to natural materials. Polyethylene.
In this test, one gram of the sample is placed with a boat at a temperature of about 500 degrees Celsius in a nitrogen gas environment for 50 minutes. At this temperature and time, polyethylene, which is a polymer material, evaporates and leaves the boat, and what remains in the boat is soot. After cooling, put the boat in the containerThe desiccant containing moisture-absorbing materials is measured by weighing scale and its calculations.
The national standard for this test for polyethylene pipes is INSO 19990.
Spreading and distributing soot
In addition to the amount of black carbon, its dispersion and distribution in polyethylene can also be important, and the uniformity of soot distribution throughout the pipe wall is one of the important quality factors. Because the excessive accumulation of soot in one part of the pipe can cause the accumulation of stress and as a result cause quality defects in that part, and on the other hand, the excessive lack of soot may cause a decrease in optical resistance in that place and thus lead to Premature drying and cracking of the wall in that part. Amorphous regions of semi-crystalline polymers are very susceptible to this degradation.
If this happens in polyethylene pipes, efforts to improve the amorphous region through molecular engineering will effectively fail and the product will lose its high performance in sunlight. gave.
It is well known that the addition of carbon black with a particle size of less than 25 nm and a concentration of 2% to 2.5% can prevent the degradation of UV tubes.
However, the polar nature of carbon black and its thermodynamic incompatibility with ethylene bridge are important factors that negatively affect the possibility of uniform dispersion of CB in polymer matrices.
Therefore, in order to ensure the uniformity of soot distribution in polyethylene, this test is performed based on the national standard of Iran INSO20059.
In order to perform this test, samples with defined standard dimensions are separated from a polyethylene pipe sample and placed between two slides, and after preparation, they are examined by an optical microscope. And with 100X magnification, we study and investigate the dispersion and distribution of black carbon in polyethylene.